In the dynamic landscape of medical technology, non-invasive catheter device innovations are not just advancements; they are lifelines that improve patient care, enhance medical procedures, and empower healthcare professionals.
Let’s delve into the world of ONEX RF's catheter tip-forming machines, exploring their features, advancements, and impact on the catheter device manufacturing industry.
A Simple Look into Catheter Tip Forming
The distal end of any catheter that directly impacts non-invasive procedures, in contact with the patient's organs, plays a critical role in its shape and functionality. It must be adequately formed without any exes extruded materials, particles, gaps, or voids to prevent injuries. ONEX RF has stepped up to the challenge by developing cutting-edge catheter tip-forming machines that redefine precision and process control.
ONEX RF's product line of catheter tipping systems offers a state-of-the-art RF generator technology for induction heating the dies in precision tip forming applications using a smaller footprint and closed loop process control.
Key Advantages for Engineers
Engineers gain numerous benefits and advantages when utilizing ONEX RF's catheter tip-forming machines.
Versatility and Adaptability
One of the key benefits is their versatility across a wide range of materials and catheter sizes. Whether working with different polymers or designing specialized catheters from 3- 34Fr or 1-75mm long, the ONEX tipping machines can meet various requirements. This adaptability empowers engineers to use the same system for multiple applications and standardize the processes utilizing a single platform without any limitations.
In-Person Training
In today's world of AI, hi-tech buzzwords do not get the job done for you, and engineers relying on the internet for solutions may only get some of the answers to perfect the manufacturing process. ONEX RF trains its customers and helps them complete their projects successfully. ONEX RF helps to use the time wisely and allows the process to be perfected.
The Shortest Die Lead-Time
ONEX RF can deliver tipping-dies in 2-3 weeks or sooner in an emergency. Based on some of our customers ' feedback, this is four times faster than a typical lead time of eight to twelve weeks compared with other suppliers. ONEX RF Catheter Tippers form up to 4" long tapered tip catheters.
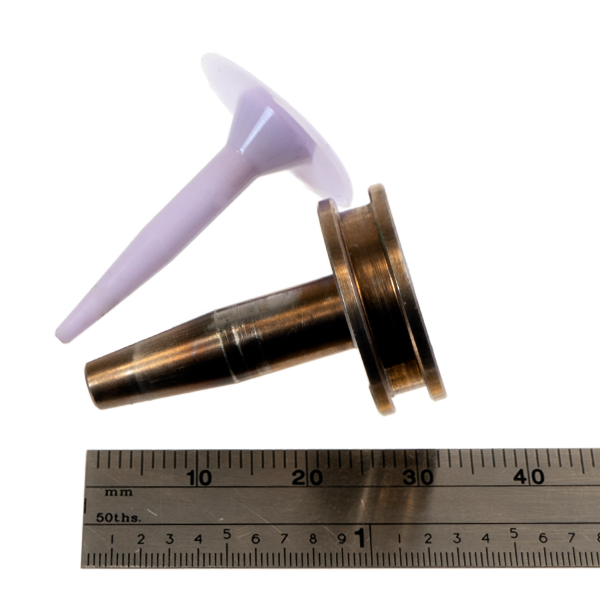
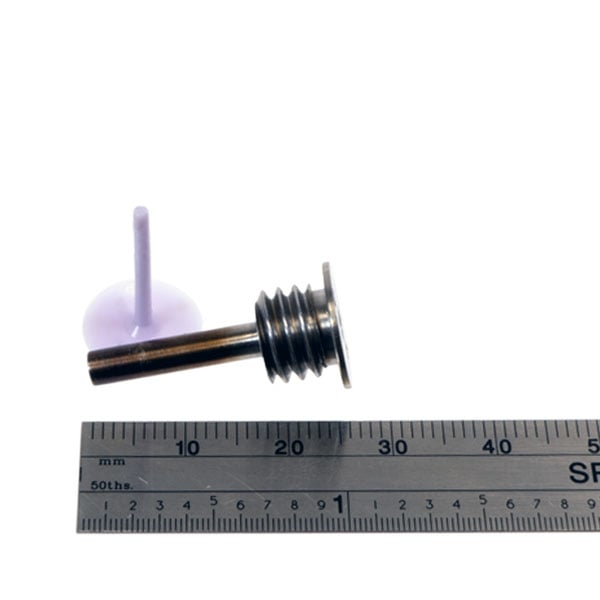
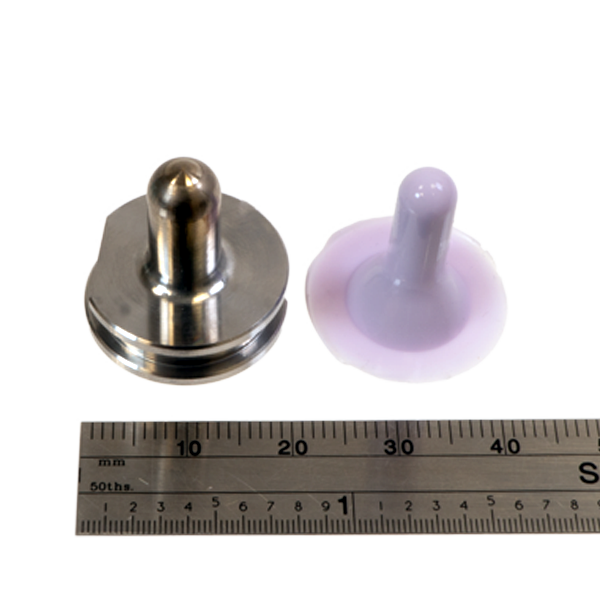
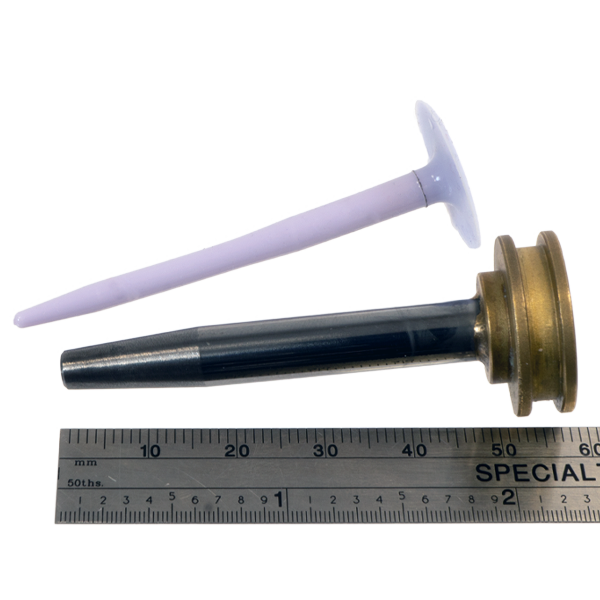
“Flash-less Tip” Manufacturing
ONEX RF offers a flash-less tipping process on some materials and sizes, reducing efforts in secondary operations to cut excess flash after the forming process. Utilizing a unique die design with precise RF energy and correct coil position control, ONEX RF may be the right solution to form the catheter tips with no flash and greater consistency.
Enhanced Precision and Consistency
Clients using ONEX RF servo catheter tip-forming machines experience a significant boost in process control, relying on precision speed control. The machine's advanced technology ensures that each catheter tip is formed with exact specifications, reducing variations and defects that might arise from using pneumatic slides.
Streamlined Process Feedback
ONEX RF's tipping systems simplify the development of the catheter tip-forming process. Each critical adjustment of a mechanical or electrical nature comes with a self-monitoring feedback signal.
The intuitive closed-loop control features help eliminate the errors caused by manual intervention of system adjustments. Plus, during process validation, the engineers can challenge the system parameters, trying various set points and dialing back to the working range effortlessly, reducing the development time.
The Future of Catheter Tip-Forming Operations
By pushing the boundaries of precision and real-time control, ONEX RF contributes to advancing catheter device manufacturing, redefining the possibilities of process control and validation.
As new catheter devices evolve, ONEX RF's commitment to innovation ensures that catheter tip forming will remain at the forefront of its RF Tip-forming technologies, ultimately leading to more process efficiency and reduced scrap in the manufacturing environment.